Aggregate Bunker
Batching Systems
It is the beginning of the “conversion to structure” story in your factory. It is the point where components from different geographies and landforms in nature, broken in different sizes and classified according to certain sizes, are stocked so that they can be weighed according to needs and taken into the system. Tens of tons of concrete aggregate that you will produce all day passes through the bunker. Despite this weight and the geographical difficulties of the region where it is located, it should have a solid construction in order to work smoothly for a long time. In addition, precise weighing must be done continuously so that the desired concrete product quality is not compromised.


Merkon is flexible as per your needs. Pit, ramp or platform, all types of bunker allocations are possible.

As per requirements of high definitive products up to 10 rooms and 50 m³ volume bunkers.
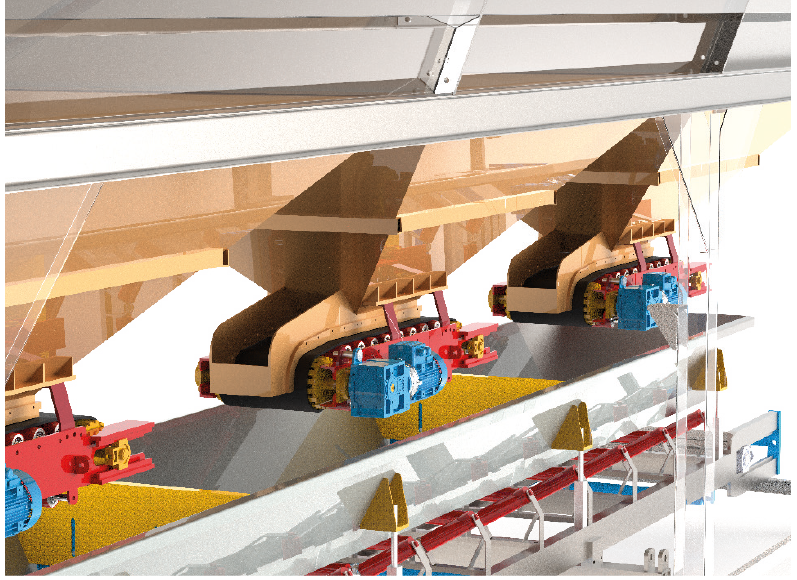
As the raw material variety in recipes increase, so does their sensitivity. Especially with the lower size aggregates, it is hard to keep the ratio correct with a wide opening gate, since the material gets poured down quickly. Pouring with a conveyor belt would make sure the system avoids faulted recipe intakes.
Big sized ingredients does takes the highest ratio of the recipe. Since every second matters in a well- functioning plant, pneumatic gate covers are simple yet smart choice in order to lower the weigh in durations of relatively bigger sized aggregate materials.
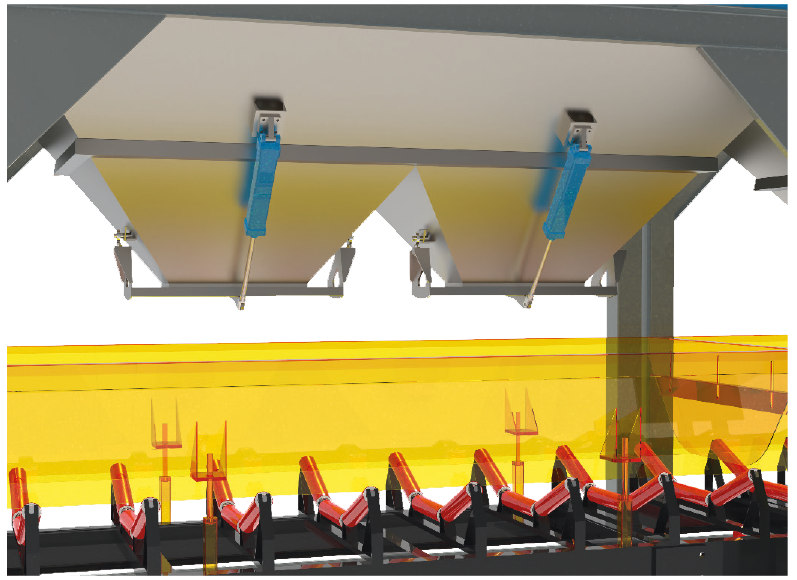
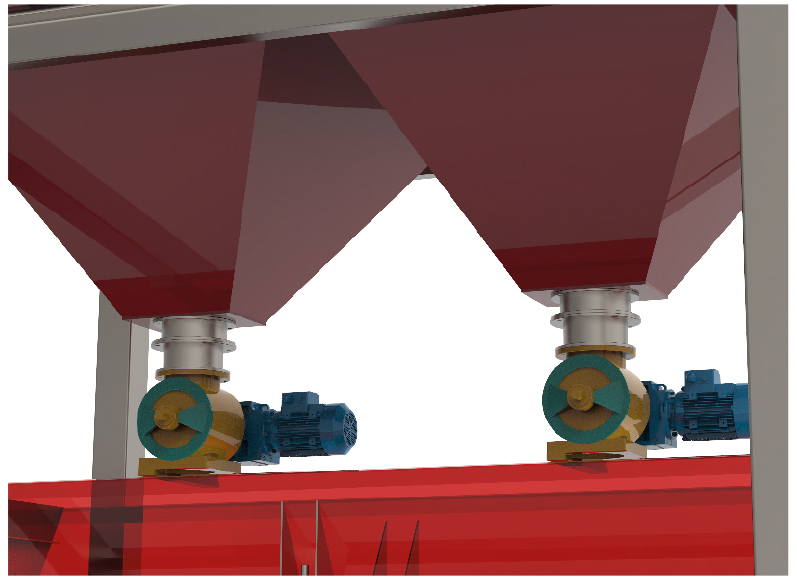
When the recipe of the batch gets ultimately sensitive, the solution to stay on top this all the time is possible by a rotary valve. Thanks to its partially segmented design, the maximum tolerance is limited from the initial design, so the perfect batch is guaranteed from day one.